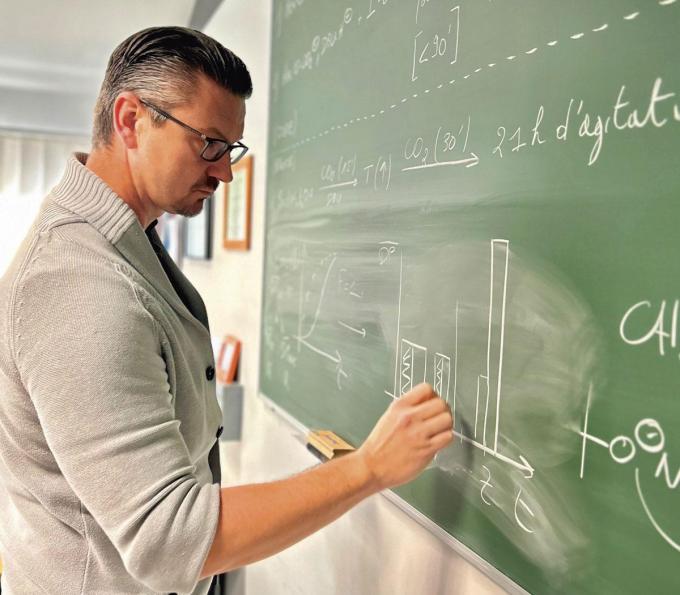
Des plastiques à base de CO2
Le dioxyde de carbone peut servir de matière première. A Mons, des chercheurs vont le séquestrer dans des plastiques recyclés à longue durée de vie. D’autres, à Anvers, visent à en faire des plastiques sans énergie fossile.
Chaque minute, dans le monde, un million de déchets plastiques, dont le temps d’utilisation moyen s’est élevé à moins d’un quart d’heure, sont jetés. En Europe, en 2018, quelque 18 millions de tonnes de plastiques usagés ont ainsi été collectés pour être traités: 18% ont été ensevelis en décharge, 40% sont partis en fumée dans un incinérateur et 42% ont rejoint l’une des deux voies de la filière des plastiques recyclés – pyrolyse ou recyclage mécanique. Ce dernier consiste à faire fondre le plastique pour soit le mouler dans une nouvelle forme, soit l’injecter dans une nouvelle matrice de polymères, formant alors un plastique partiellement composé de matière recyclée. «Qu’il s’agisse de la mise en décharge, de l’incinération ou du recyclage, toutes ces méthodes ont des conséquences délétères de par leurs rejets de quantités variables, mais massives, de CO2 dans l’atmosphère, indique Olivier Coulembier, maître de recherches FNRS au service des matériaux polymères et composites de l’UMons. Ainsi, deux tonnes de plastique traitées par voie mécanique – la voie de recyclage la plus utilisée – libèrent presque une tonne de dioxyde dans l’atmosphère. Par ailleurs, ce type de recyclage s’essouffle vite: il requiert de chauffer le plastique à 150-250°C, ce qui engendre une dégradation du polymère, laquelle se répercutera négativement sur les propriétés finales du matériau. Ce n’est donc pas la panacée.»
Grâce à la subvention d’un million d’euros que lui a récemment accordé le Fonds AXA pour la recherche, Olivier Coulembier entend développer un nouveau concept de recyclage. Celui-ci séquestrera du gaz carbonique dans le plastique recyclé à la suite de réactions menées à basse température, pour économiser l’énergie. «Nous allons développer une voie de recyclage à l’empreinte carbone la plus faible possible, voire nulle. Et pourquoi pas négative?! L’ émission de CO2 en fin de course sera alors inférieure à la quantité de CO2 utilisée au début du processus de recyclage.»
Température ambiante et catalyse organique
L’idée principale est donc d’incorporer du CO2 au plastique à recycler. Pour ce faire, le dioxyde sera d’abord converti en sels de carbonate, selon une réaction simple, en une seule étape, connue depuis longtemps. Mais alors que celle-ci est généralement réalisée à hautes pressions et températures en présence de catalyseurs métalliques toxiques, le laboratoire montois exploitera son expertise et utilisera des petites molécules organiques non toxiques en guise de catalyseurs. Et ce, à température et pression ambiantes.
Ces sels de carbonate et de structures moléculaires diverses iront ensuite se lier aux points d’ancrage que les chercheurs implanteront sur les macromolécules de plastique à recycler. « A haute température de réaction, les additifs et colorants présents dans le plastique à recycler facilitent la dégradation de ce dernier. Afin d’éviter cette dégradation, et ainsi garder les propriétés intrinsèques du matériau, nous travaillerons à la température la plus basse possible. Grâce, à nouveau, à la catalyse organique, nous devrions pouvoir y arriver.»
Au final, quel pourrait être l’usage du matériau recyclé produit en fin de processus? «Ce qui serait fantastique, et contribuerait à ralentir les changements climatiques, ce serait de l’utiliser comme matériau de construction. En effet, séquestré de la sorte, on estime qu’il faut un million d’années au CO2 pour regagner l’atmosphère!» A titre de comparaison, du dioxyde de carbone transformé en carburant de synthèse est rejeté dans l’air un an à peine après en avoir été extrait.
Sans pétrole mais identique
Regroupés au sein de la spin-off Oxylum, des chimistes anversois viennent de réussir un véritable tour de force: fabriquer, à partir du seul CO2, de l’acide formique – ingrédient essentiel à la chimie industrielle, jusqu’alors produit au départ de gaz naturel. D’ici à 2025, ils souhaitent disposer d’une première installation pilote capable de convertir jusqu’à 2 000 tonnes de CO2 en acide formique. Idéalement, elle serait sise dans le cluster industriel du port d’Anvers, ce qui permettrait de convertir le CO₂ d’une usine en produits immédiatement utilisables dans le port. Leur astuce? «En nous appuyant sur plus d’une décennie de recherche en électrochimie, nous avons mis au point des catalyseurs et des réacteurs de pointe pour réaliser cette réaction dans les conditions les plus optimales», souligne Bert De Mot, CEO d’Oxylum. Cette nouvelle technologie électrochimique, il souhaite la faire évoluer pour parvenir à produire de l’éthylène à partir du seul CO2. Et ce, afin de permettre la synthèse de polymères d’éthylène, la matière plastique la plus commune, sans avoir recours aux énergies fossiles. Certes, « il existe déjà des bioplastiques mais leurs propriétés ne sont pas identiques à celles du plastique à base de pétrole, ce qui pose des problèmes. Nous avons comme objectif de fabriquer des plastiques moléculairement identiques à ceux conçus au départ de pétrole, mais en n’utilisant que du CO2.»
Vous avez repéré une erreur ou disposez de plus d’infos? Signalez-le ici