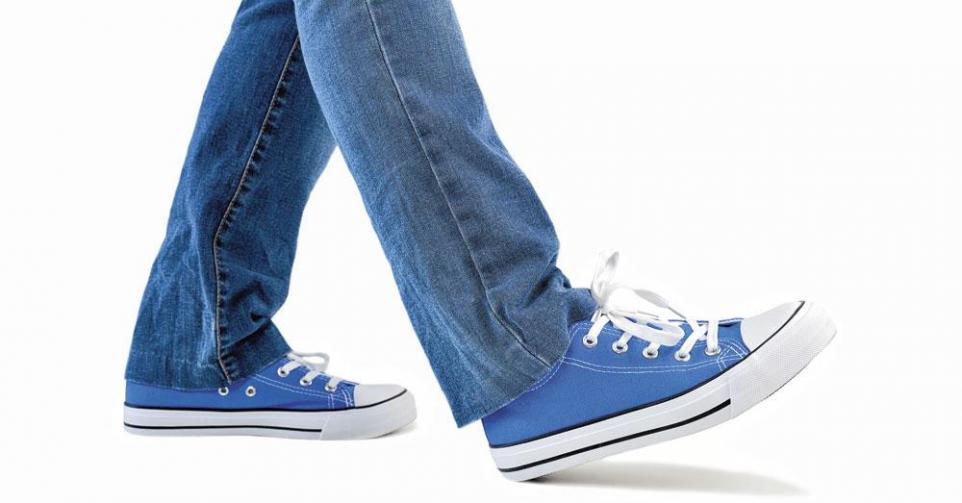
Resortecs: le fil « magique » bruxellois qui pourrait révolutionner l’industrie textile
Lancée en 2017, la start-up bruxelloise Resortecs entend sortir l’industrie textile de ses engrenages destructeurs en facilitant le démontage des vêtements et donc le recyclage. Grâce à un fil qui disparaît comme par magie.
Les statistiques sont accablantes. Avec 1,2 milliard de tonnes d’émission de CO2 et 34 millions de tonnes de déchets par an, l’industrie textile figure dans le top 5 des secteurs les plus polluants du monde. Et la situation s’aggrave puisque sur le continent asiatique, les nouvelles classes moyennes sont en train de succomber elles aussi à la fast fashion : des vêtements vite produits, vite achetés, vite portés, vite jetés. Dans plusieurs endroits du monde, comme dans le désert de l’Atacama, au Chili, des décharges sauvages croissent sous l’effet de cette mode jetable.
Pourtant, des solutions existent, qui creusent de nouvelles logiques de production et de consommation. Des trouvailles techniques se développent pour briser cette linéarité dévastatrice et entrer dans une circularité vertueuse. Parmi celles-ci, Smart Stitch™ et Smart Disassembly™, deux innovations mises au point par la start-up bruxelloise Resortecs, pourraient bien révolutionner le monde de la mode.
“Le but de Resortecs, c’est de faciliter le recyclage textile en travaillant sur un des problèmes-clés : le démontage. Car pour recycler un vêtement, il faut d’abord éliminer tous les boutons, fermetures éclair, étiquettes et autres composants accrochés au tissu, explique Cédric Vanhoeck, 30 ans, cofondateur de la société avec Vanessa Counaert. Aujourd’hui, pour démonter les vêtements de manière qualitative, il n’y a que la méthode manuelle. D’autres systèmes, automatiques, mécaniques, détruisent le tissu ou ne permettent pas d’obtenir une bonne qualité ou une pureté suffisante dans le tri. »
L’idée géniale de Resortecs est de proposer un fil thermofusible, baptisé Smart Stitch™, qui sert de fil de couture dans la confection des vêtements, sur le principe design-for-disassembly (« conçu pour être démonté ») et qui ensuite, dans le processus de recyclage, s’éliminera de lui-même, sans manipulation, grâce à la chaleur d’un four spécifique, appelé lui Smart Disassembly™. Sur les vidéos présentant le procédé, cette disparition du fil semble presque magique ! Dans le recyclage industriel, le tissu ainsi récupéré sera retransformé en fibre, puis en fil, puis à nouveau en tissu, bouclant ainsi la boucle.
Resortecs mise sur l’éphémère mais le durable
Pour Cédric Vanhoeck, la prise de conscience de la nécessité de l’économie circulaire a eu lieu à la Technische Universiteit de Delft, où il étudiait l’ingénierie du design industriel. C’est une des premières universités à avoir rejoint la Fondation Ellen MacArthur, fondée en 2009 par la célèbre navigatrice britannique et porte-drapeau d’un futur repensé grâce à l’économie circulaire.
A Delft, le jeune entrepreneur a été sensibilisé à l’urgence de systèmes de production où, comme dans la nature, les déchets servent de matière première à la recréation de nouveaux objets. Ces principes, popularisés par des ouvrages comme Cradle to Cradle – créer et recycler à l’infini de Michael Braungart et William McDonough, ou le concept de Blue economy du Belge Gunter Pauli (2010), Cédric Vanhoeck les a emportés avec lui lors de ses études en marketing à la Domus Academy de Milan puis en mode à l’Académie d’Anvers.
« A Anvers, j’ai réalisé que, contrairement à ce que les gens pensaient, les créateurs ne pourraient pas mener eux-mêmes leur transition au niveau du design des vêtements, se rappelle-t-il. Ce n’était pas possible. Mais en utilisant les principes du design-for-disassembly, on peut produire un fil qui permet au créateur de continuer à travailler de la même manière tout en produisant des vêtements facilement démontables. »
Resortecs propose trois types de fils, disponibles en différentes couleurs et différentes épaisseurs, qui se dissolvent respectivement à 150, 170 et 190 degrés, pour coudre des vêtements, des accessoires ou des matelas, en gardant les mêmes machines et sans différence visuelle au niveau du résultat. Ce type de fil fabriqué à partir de polymères était déjà utilisé dans l’industrie textile, mais plutôt comme fixation temporaire, pour des broderies par exemple. Le concept est ici de l’utiliser dans le produit final, avec l’objectif de facilitation du démontage. « La technologie existait, mais plutôt en envisageant une augmentation de la production et pas forcément la dynamique de la circularité, de l’écologie, de la durabilité », souligne Davidson Leite, responsable de la communication et du branding.
Pré- et post-consommation
Pour bien se représenter le potentiel de cette innovation, il faut savoir que le prototype du four de désassemblage de Resortecs a une capacité maximum de 1 tonne de vêtements par jour, soit l’équivalent de 2000 jeans. « Dans ce cas, c’est un procédé discontinu, comme un four de cuisine qu’on ouvre et qu’on ferme, précise William Allouche, responsable technique du désassemblage chez Resortecs. Mais la prochaine version du four sera une version continue, où les vêtements sortiront désassemblés sans interruption. Pour arriver à 10 tonnes, 20 000 jeans par jour. » Dix tonnes, c’est-à-dire le poids à partir duquel le processus de recyclage devient avantageux pour l’industrie.
Des chiffres qui donnent le tournis, mais qui sont proportionnels au gigantisme de la production textile. « Des marques dans le segment premium comme Timberland, Tommy Hilfiger ou Calvin Klein produisent chacune en moyenne 5 millions de jeans par an pour l’Europe, signale Cédric Vanhoeck. Pour des marques de fast fashion comme Primark ou H&M, c’est quatre fois plus, soit 20 millions de jeans. » Toujours dans le cas du jeans, Resortecs a calculé que sa méthode de désassemblage permettait de diminuer les émissions de CO2 de 50 %, les déchets de 80 % et l’utilisation d’eau de 90 %. Sans compter la diminution des produits toxiques utilisés dans la fabrication, notamment lors de la teinture du tissu. « On préserve ainsi des ressources naturelles qui se raréfient, comme l’eau ou le coton, relève Christophe Berlo, responsable financier. Avec des optimisations collatérales : du champ de coton au jeans, on perd 50 % de matière première, et encore 15 % de rétrécissement lors du premier lavage. » Recycler le tissu représente dès lors un gain non négligeable, même dans un monde idéal où la mode serait plus « slow ».
Avec son procédé, Resortecs vise pour l’instant principalement les déchets dit « pre-consumer waste » (déchets de pré-consommation), c’est-à-dire les vêtements avec des défauts qui n’ont pas été mis sur le marché et les invendus. Une proportion qui peut s’étendre de 5 à 45 % de la production du prêt-à-porter, avec une moyenne autour de 15 %. Or, le seuil à dépasser pour que le recyclage soit rentable est de 30 %. Ce qui veut dire que les marques doivent également investir dans les retours de vêtements, pour agir sur le « post-consumer waste » (déchets de postconsommation, c’est-à-dire les vêtements déjà portés). « C’est à la fois la beauté et la difficulté de cette solution : plus on récupère de vêtements, plus on gagne d’argent, qu’on pourra ensuite réinvestir dans des systèmes de reprise », conclut Cédric Vanhoeck.
Le défi est donc énorme, et le chemin encore long. Mais la transition est enclenchée. Depuis fin 2019, la marque américaine de jeans sur mesure Unspun produit les modèles « Genesis » avec le fil Resortecs. En novembre dernier, H&M sortait une collection capsule « A Circular Design Story » comprenant cinq articles avec ce fil. Et à la fin de cette année, le géant français Decathlon lancera un premier modèle à grande échelle -une veste de ski- avec Resortecs. Les prémices d’un indispensable changement de paradigme.
Vous avez repéré une erreur ou disposez de plus d’infos? Signalez-le ici